Introduction
Differential pressure (dp) flow measurement is a common and widely used technique in various industries to determine the flow rate of liquids and gases within a pipeline or system. This method relies on the principle that the difference in pressure across a flow element, such as an orifice plate or a venturi tube, is directly proportional to the flow rate.
Differential pressure (dp) flow measurement can be used for a wide range of fluid types, including liquids and gases, and is suitable for various industries, including oil and gas, water treatment, and manufacturing.
How Flow Elements Work
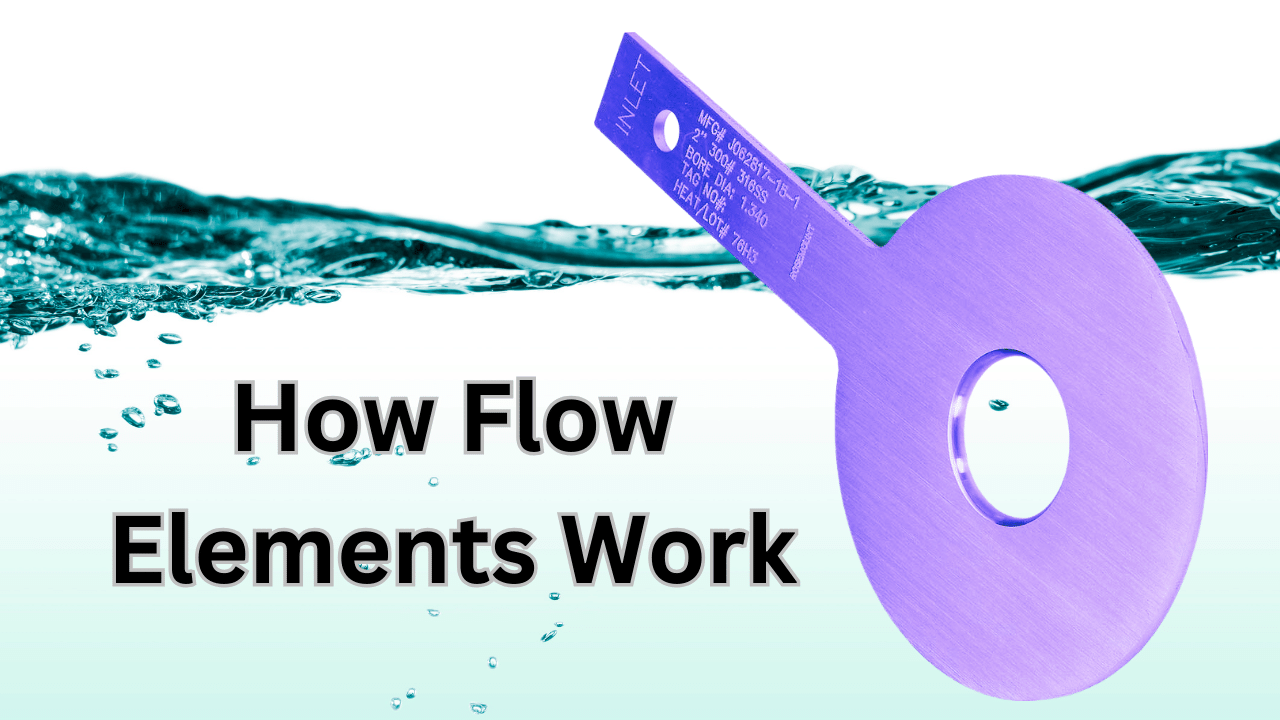
Bernoulli’s Principle: At the heart of flow element operation lies Bernoulli’s principle, which states that as the speed of a fluid increases, its pressure decreases. Flow elements exploit this principle to measure flow rates accurately. When fluid flows through a constricted area (as in an orifice plate or venturi tube), its speed increases, resulting in a pressure drop. By measuring this pressure drop, engineers can calculate the flow rate.
Differential Pressure Measurement: Flow elements typically incorporate differential pressure sensors that measure the pressure drop across the element. This pressure difference is directly proportional to the flow rate, allowing for precise calculations.
How differential pressure (dp) flow measurements work
Flow Element Installation: To begin the process of measuring flow using differential pressure (dp), a flow element is installed within the pipeline or conduit through which the fluid is flowing. Common types of flow elements include orifice plates, venturi tubes, flow nozzles, and pitot tubes.
Pressure Taps: Pressure taps are small openings or ports strategically placed before and after the flow element. These taps allow for the measurement of the pressure differential across the flow element. One tap is located upstream (before) the flow element, and the other is located downstream (after) it.
Pressure Differential: As the fluid flows through the flow element, it encounters a constriction or restriction, causing a change in the flow velocity. According to Bernoulli’s principle, an increase in fluid velocity results in a decrease in pressure. Therefore, the pressure upstream of the flow element is higher than the pressure downstream.
Measurement: Pressure transmitters or gauges are connected to the pressure taps to measure the pressure on both sides of the flow element. These measurements are typically in units of pressure, such as pounds per square inch (psi) or pascals (Pa).
Calculation: The pressure differential, ΔP (Delta P), is calculated by subtracting the downstream pressure from the upstream pressure. This ΔP value is directly related to the flow rate and is used in flow rate calculations.
Flow Rate Calculation: Using the known properties of the flow element and the fluid being measured, engineers and technicians can use specific equations to convert the pressure differential into an actual flow rate. The choice of equation depends on the type of flow element and the characteristics of the fluid.
Output Display: The calculated flow rate is typically displayed on a flow transmitter or a central control system. It can be expressed in various units, such as gallons per minute (GPM), cubic meters per hour (m³/h), or standard cubic feet per minute (SCFM), depending on the application.
Advantages of Differential Pressure (dp) Flow Measurement

Wide Applicability: Differential pressure (dp) flow measurement is highly versatile and can be used for measuring the flow of various fluids, including liquids and gases. It finds applications in diverse industries such as oil and gas, water treatment, chemical processing, and HVAC systems.
Cost-Effective: It is often a cost-effective method of flow measurement, particularly for large pipelines and industrial processes. The equipment required for differential pressure (dp) measurement is typically more affordable than some other flow measurement techniques.
High Accuracy: When properly calibrated and maintained, differential pressure (dp) flow measurement can provide high levels of accuracy. This makes it suitable for applications where precise flow rate control and measurement are critical.
Reliability: The method is known for its reliability and robustness. Many flow elements used in differential pressure (dp) measurement have no moving parts, reducing the risk of mechanical failure.
Real-time Monitoring: Differential pressure (dp) flow measurement allows for real-time monitoring and control of fluid flow. This capability enables operators to make immediate adjustments to maintain desired flow rates and ensure process efficiency.
Low Maintenance: Due to the absence of moving parts in many flow elements, maintenance requirements are often minimal. This reduces downtime and operational costs associated with maintenance activities.
Steady State Measurement: It excels in measuring steady-state flow conditions, where the flow rate remains relatively constant over time. This is particularly useful in applications where consistent flow rates are required.
Compatibility with Various Flow Elements: Differential pressure (dp) flow measurement can be adapted to suit different flow element designs, including orifice plates, venturi tubes, and flow nozzles, depending on the specific application and measurement requirements.
Ease of Installation: The installation of differential pressure (dp) flow measurement systems is relatively straightforward and well-documented. Many standard flow element configurations are available, making it easier to select the appropriate design for a given application.
Applicable to Various Industries: This method is used in a wide range of industries, from industrial processes and utilities to research and development. Its adaptability makes it suitable for different sectors and applications.
Compatibility with Existing Systems: Differential pressure (dp) flow measurement can often be integrated into existing systems with minimal modifications, making it a practical choice for retrofitting older equipment.
Diagnostics: Modern differential pressure (dp) flow measurement systems may include diagnostic capabilities that help identify issues or anomalies in the flow process, facilitating proactive maintenance.
These advantages make differential pressure (dp) flow measurement a valuable tool in many industrial and commercial settings where accurate and reliable flow rate measurements are essential for operational efficiency, quality control, and safety.
Disadvantages of Differential Pressure (dp) Flow Measurement
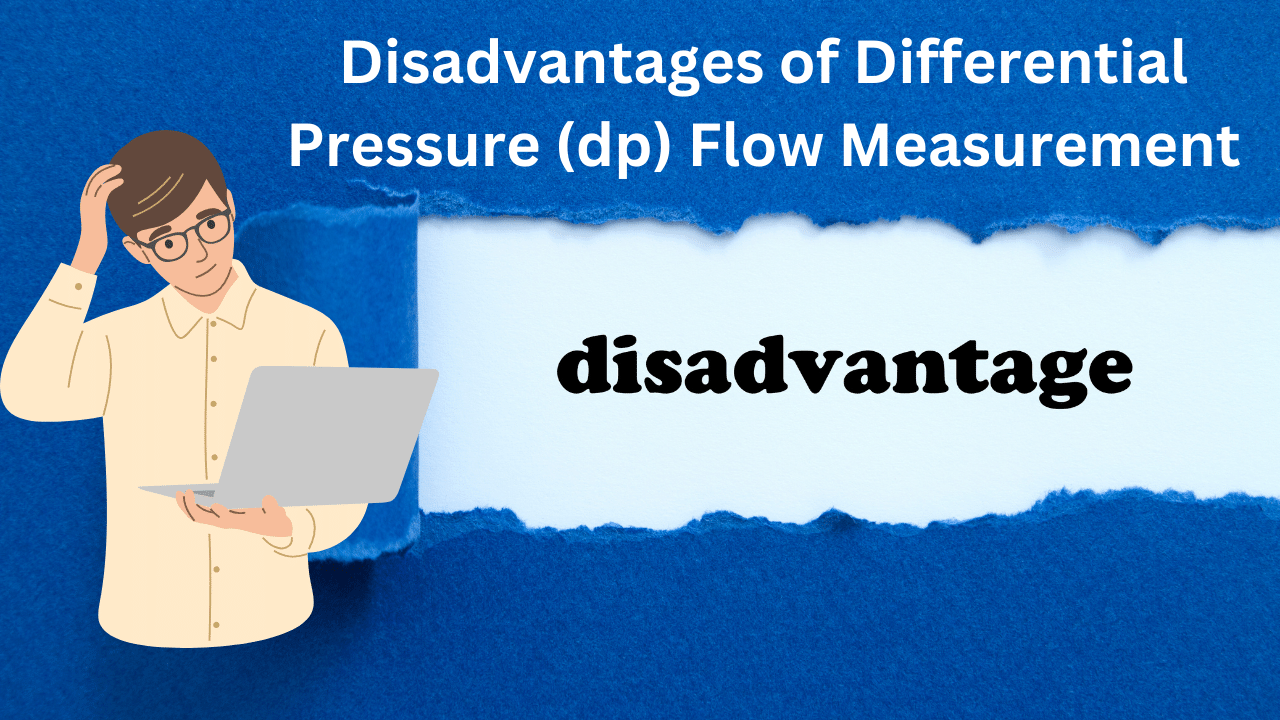
Limited Turndown Ratio: One of the primary disadvantages of differential pressure (dp) flow measurement is its limited turndown ratio. Turndown ratio refers to the range of flow rates over which the measurement remains accurate. In many cases, this range can be relatively narrow, making it less suitable for applications with widely varying flow rates.
Pressure Loss: The presence of flow elements like orifice plates or venturi tubes can result in a significant pressure drop across the measurement device. This pressure loss can be undesirable, especially in systems where maintaining high pressure is crucial.
Inaccuracy for Non-Ideal Fluids: Differential pressure (dp) flow measurement assumes that the fluid behaves ideally, which may not always be the case. Non-ideal fluids, such as those with high viscosity or compressibility, can lead to measurement inaccuracies.
Calibration and Maintenance: Maintaining the accuracy of a differential pressure (dp) flow measurement system requires regular calibration and maintenance. Over time, factors like wear and tear or changes in fluid properties can affect measurement accuracy.
Complexity in Calculation: Calculating flow rates based on differential pressure (dp) measurements can be complex and may require knowledge of fluid properties, flow element characteristics, and equation manipulation. This complexity can lead to errors if not performed correctly.
Sensitivity to Pipe Conditions: The accuracy of differential pressure (dp) measurements can be sensitive to the condition of the pipeline, including pipe roughness and the presence of bends or obstructions. These factors can introduce measurement errors.
Limited Applicability for Multiphase Flows: Differential pressure (dp) flow measurement is less suitable for multiphase flows where the fluid consists of a combination of gases and liquids. The measurement can become challenging when dealing with such complex flow conditions.
Temperature Effects: Variations in fluid temperature can affect the accuracy of differential pressure measurements, as temperature can alter fluid properties like density and viscosity. Compensation for temperature effects may be necessary.
Complex Installations: Installing and configuring differential pressure (dp) flow measurement systems can be more complex compared to some other flow measurement methods. Proper installation is crucial for accurate measurements.
Cost of Instruments: While differential pressure (dp) flow measurement can be cost-effective in some cases, high-quality pressure transmitters and differential pressure sensors can be relatively expensive, impacting the overall cost of the measurement system.
Despite these disadvantages, differential pressure (dp) flow measurement remains a widely used and valuable method for many applications due to its reliability, versatility, and ability to provide real-time flow data. Engineers and technicians often weigh these disadvantages against the specific requirements and conditions of their applications to determine if it is the most suitable flow measurement technique.
Frequently Asked Questions (FAQs)
Q1. Are flow elements only used for measuring flow rates?
A1. Flow elements are primarily used for measuring flow rates, but they also find applications in flow control and regulation.
Q2. How do I choose the right flow element for my application?
A2. The choice of flow element depends on factors like the type of fluid, flow rate, and the required level of accuracy. Consulting with a flow measurement expert is advisable.
Q3. Can flow elements be used in extreme temperatures and pressures?
A3. Yes, flow elements can be designed to withstand extreme temperatures and pressures, making them suitable for a wide range of operating conditions.
Q4. Are flow elements compatible with digital data acquisition systems?
A4. Yes, modern flow elements can be integrated with digital data acquisition systems for real-time monitoring and control.
Q5. What are the maintenance requirements for flow elements?
A5. Regular calibration and maintenance are essential to ensure the continued accuracy and reliability of flow elements. It’s important to follow manufacturer recommendations for upkeep.