Introduction
In the world of temperature measurement, RTD sensors are a well-known and reliable technology. But what exactly is an RTD sensor, and how does it work? This article dives deep into the world of RTD sensors, their advantages, applications, and everything you need to know about these remarkable temperature-sensing devices.
What is RTD Sensor | Understanding RTD Sensors
RTD stands for Resistance Temperature Detector. These sensors are known for their high accuracy in temperature measurement. They rely on the principle that the electrical resistance of a material changes predictably with temperature. RTD sensors are widely used in industrial and scientific applications where precision is crucial.
How RTD Sensors Work
RTD sensors operate on the fundamental concept that the electrical resistance of a material increases linearly with temperature. The most common material used in RTD sensors is platinum, known for its stable and consistent resistance-temperature relationship. As the temperature changes, the electrical resistance of the platinum wire in the sensor changes, which can be measured accurately to determine the temperature.
Applications of RTD Sensors
RTD sensors find applications in a wide range of industries, including aerospace, pharmaceuticals, automotive, oil and gas, petrochemical and food processing. They are used in processes where precise temperature control is essential, such as in laboratories, manufacturing, and climate control systems.
Types of RTD Sensors
RTD (Resistance Temperature Detector) sensors are commonly used to measure temperature by correlating the resistance of the RTD element with temperature. There are several types of RTD sensors based on the materials used for the sensing element. The most common types include:
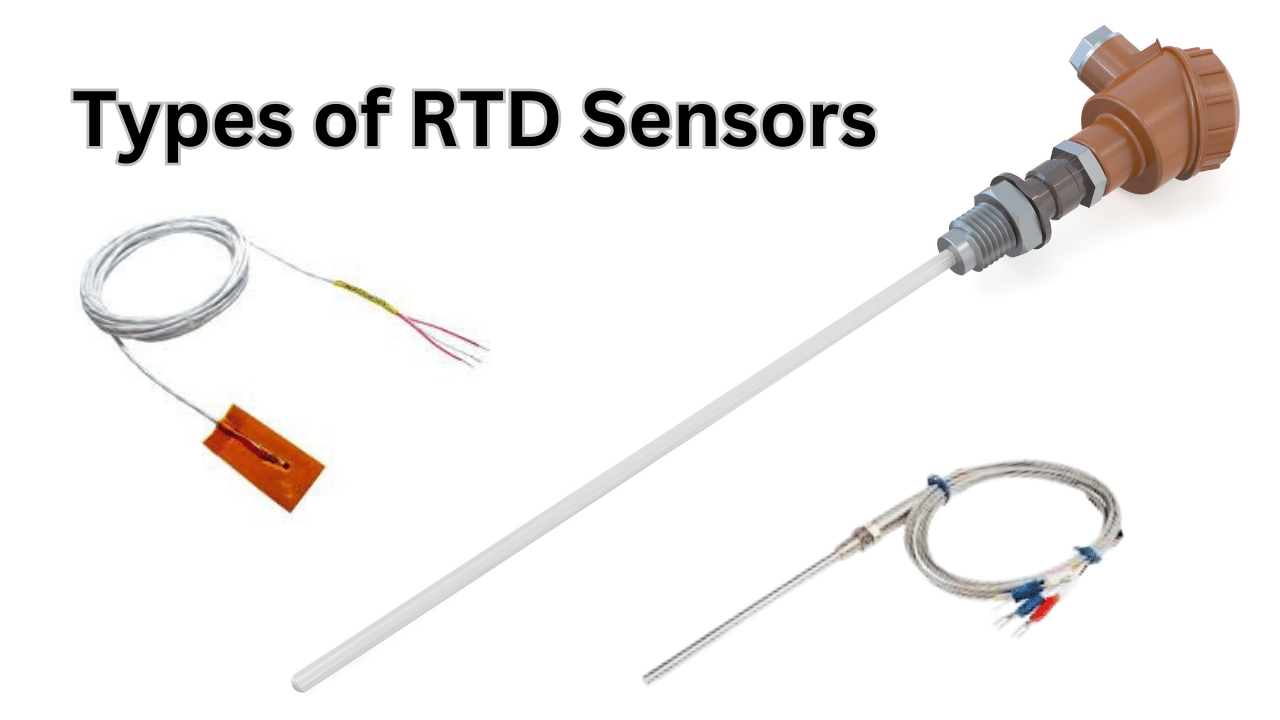
Platinum RTD (Pt RTD)
- Platinum RTDs are the most widely used RTD sensors due to their excellent stability and linearity.
- They are typically made of platinum wire wound on a ceramic or glass core.
- The most common type of Pt RTD is the Pt100, where the resistance at 0°C is 100 ohms. Other variations include Pt1000, where the resistance at 0°C is 1000 ohms.
Nickel RTD (Ni RTD)
- Nickel RTDs are less common than platinum RTDs but are still used in certain applications.
- They are generally less accurate and stable than platinum RTDs.
- Nickel RTDs are typically made of nickel or nickel-iron alloys.
Copper RTD (Cu RTD)
- Copper RTDs are less common and are usually used in specialized applications.
- They are less stable and have a limited temperature range compared to platinum RTDs.
- Copper RTDs are typically made of copper wire.
Balco RTD
- Balco (Bimetallic Alloy) RTDs are made of a combination of two different metals or alloys.
- They are known for their self-heating properties, which can be useful in certain applications.
- Balco RTDs have a resistance that changes with temperature.
Thin-Film RTD
- Thin-film RTDs are constructed by depositing a thin layer of platinum or another temperature-sensitive material onto a ceramic substrate.
- They are compact and have a fast response time but may be less accurate than wire-wound RTDs.
Wire-Wound RTD
- Wire-wound RTDs are constructed by winding a length of fine wire (usually platinum) around a ceramic or glass core.
- They are known for their accuracy and stability.
- Wire-wound RTDs are bulkier compared to thin-film RTDs.
Surface RTD
- Surface RTDs are designed to be placed directly on the surface of the object or medium being measured.
- They are often used in applications where contact with the medium is not possible or desirable.
Each type of RTD sensor has its own set of advantages and limitations, and the choice of sensor type depends on the specific requirements of the temperature measurement application. Platinum RTDs, particularly the Pt100 and Pt1000, are the most commonly used due to their high accuracy and stability over a wide temperature range.
Calibration of RTD Sensors
Calibration of RTD (Resistance Temperature Detector) sensors is a crucial process to ensure their accuracy and reliability in temperature measurement. Calibration involves comparing the sensor’s output to a reference standard at various known temperatures and making necessary adjustments. Here’s a general overview of the calibration process for RTD sensors:
Prepare Calibration Equipment
- You will need a precision temperature reference source, often a calibrated thermometer or temperature bath, to provide known temperature values.
- Ensure that the calibration equipment is properly set up and functioning accurately.
Stabilize the RTD Sensor
- Before calibration, allow the RTD sensor to reach thermal equilibrium with the environment to ensure accurate readings. This typically involves waiting until the sensor and its surroundings are at the same temperature.
Record the Initial Resistance
- Measure and record the resistance of the RTD sensor at a known reference temperature. The reference temperature should be within the sensor’s specified range.
Establish a Calibration Curve
- Create a calibration curve or table that relates the measured resistance of the RTD sensor to the reference temperature. This curve can be linearized for more accurate temperature conversion.
Perform Calibration Points
- At various reference temperatures, measure the RTD’s resistance and compare it to the expected resistance based on the calibration curve.
- Adjust the sensor or the associated measurement system as needed to minimize the difference between the measured and expected resistance values.
Interpolation and Extrapolation
- For temperatures between calibrations points, use interpolation to estimate the resistance and, subsequently, the temperature.
- Be cautious when extrapolating beyond the calibration points, as accuracy may decrease.
Document Calibration Data
- Keep thorough records of the calibration process, including the reference temperatures, measured resistance values, and any corrections or adjustments made.
Repeat as Needed
- Depending on the application and the level of accuracy required, you may need to perform multiple calibration points and iterations.
Certify and Document
- Once you are satisfied with the calibration results, certify the RTD sensor as accurately calibrated.
- Document the calibration process, including the calibration curve and any adjustments made.
Regular Maintenance
- RTD sensors should be recalibrated periodically, as their accuracy may change over time due to factors like drift, contamination, or physical damage.
Traceability
- Ensure that the reference standards used for calibration are traceable to a recognized national or international standard to maintain confidence in the calibration process.
Calibration Certificates
- Some industries and applications may require calibration certificates to provide proof of accuracy and traceability for regulatory compliance or quality control.
Calibration is a critical step in maintaining the accuracy of RTD sensors, and it is essential for ensuring the reliability of temperature measurements in various industrial and scientific applications.
Selecting the Right RTD Sensor
Selecting the right RTD (Resistance Temperature Detector) sensor is crucial for accurate temperature measurement in various applications. RTD sensors are known for their high accuracy and stability, making them a popular choice in many industries. Here are the key factors to consider when selecting an RTD sensor:
Temperature Range
- Determine the temperature range within which you need to measure. RTD sensors are available in various types, such as Pt100 (platinum 100 ohm), Pt1000, or other materials like copper and nickel. Ensure that the sensor’s range matches your application’s temperature requirements.
Accuracy
- RTD sensors offer high accuracy, with the most common Pt100 sensor providing accuracy within a few tenths of a degree Celsius. Consider the required level of precision for your application and choose an RTD sensor with an appropriate accuracy rating.
Sensing Element Material
- Platinum is the most common material for RTD sensing elements due to its excellent stability and linearity. Pt100 and Pt1000 sensors are widely used. However, other materials like nickel or copper RTDs may be suitable for specific applications. Choose the material that best fits your needs.
Response Time
- Consider the response time required for your application. RTDs generally have a slower response time compared to thermocouples. Ensure the sensor can provide temperature readings at the desired rate.
Environmental Conditions
- Assess the environmental conditions in which the RTD sensor will operate. Factors like humidity, chemical exposure, and pressure can affect sensor performance. Select a sensor that is compatible with your specific environmental conditions.
Mounting and Installation
- Choose a sensor with a suitable form factor and mounting options for your application. RTD sensors come in various configurations, including probe-type, surface-mounted, and immersion sensors. Ensure the selected sensor can be easily installed in your system.
Calibration
- RTD sensors may require calibration to ensure accurate temperature readings. Determine if the sensor comes with a calibration certificate, and if not, plan for calibration procedures in your application.
Longevity and Durability
- Consider the expected lifespan of the RTD sensor. Platinum-based RTDs are known for their long-term stability. Ensure the sensor can withstand the expected operational conditions and has a long service life.
Cost
- Compare the cost of different RTD sensors within your budget while balancing accuracy and performance. Cheaper RTD sensors may sacrifice accuracy and durability, so be cautious when choosing based solely on cost.
Compatibility
- Ensure the selected RTD sensor is compatible with your measurement system, data acquisition equipment, or control system. Check the sensor’s output type (e.g., 2-wire, 3-wire, 4-wire) and interface with your instrumentation.
Selecting the right RTD sensor involves considering factors like temperature range, accuracy, sensing element material, response time, environmental conditions, installation requirements, calibration, longevity, cost, and compatibility with your system. Careful consideration of these factors will help you choose the most suitable RTD sensor for your specific application.
Conclusion
In summary, RTD sensors are vital components in temperature measurement and control, offering precision, durability, and versatility across various industries. Understanding their working principles, types, applications, and proper usage is essential for anyone involved in temperature measurement and control.
Frequently Asked Questions (FAQs)
Q1. How accurate are RTD sensors?
A1. RTD sensors are known for their high accuracy, typically within a few tenths of a degree Celsius.
Q2. Can RTD sensors be used in extreme temperatures?
A2. Yes, RTD sensors can be used in both extremely high and low-temperature environments.
Q3. What is the typical lifespan of an RTD sensor?
A3. With proper care and maintenance, RTD sensors can last for many years, often a decade or more.
Q4. Are RTD sensors affected by electromagnetic interference?
A4. RTD sensors are relatively immune to electromagnetic interference, making them suitable for industrial environments with electronic noise.
Q5. How do I calibrate an RTD sensor?
A5. Calibrating an RTD sensor typically involves comparing its readings to a known temperature source, and adjustments can be made to ensure accuracy.
1 thought on “What is rtd sensor?”