Introduction
Pressure is a fundamental parameter in the world of engineering and industry. From maintaining the integrity of pipelines to ensuring the efficient operation of heavy machinery, understanding and monitoring pressure is crucial for safe and optimal functioning. This is where pressure gauges come into play. A pressure gauge is a vital instrument used to measure the pressure of gases or liquids in various systems.
In this article, we will delve into the significance of pressure gauges in industrial applications, their types, working principles, including various pressure elements, and the historical journey that has led to their indispensable role in today’s industries.
Mathematically, Pressure defined as
Pressure = Force / Area
In simpler terms, pressure is the amount of force applied perpendicular to a unit area of a surface. The SI (The International System of Units) unit of pressure is the Pascal (Pa), which is equivalent to one newton of force per square meter of area:
1 Pa = 1 N/m²
Pressure can be experienced in various contexts, such as in fluids (liquids and gases) and solids. For example:
Fluid Pressure: In a fluid (liquid or gas), pressure is exerted in all directions due to the random motion of molecules. This is why you might feel pressure in all directions when you’re submerged underwater or in a compressed gas environment.
Atmospheric Pressure: The weight of the Earth’s atmosphere above us creates atmospheric pressure. At sea level, standard atmospheric pressure is around 101.3 kPa (kiloPascals), which is roughly equivalent to 14.7 pounds per square inch (psi).
Hydrostatic Pressure: In a fluid column (like water in a container), the pressure increases with depth due to the weight of the fluid above. This is why water pressure is higher at greater depths.
Pressure in Solids: Pressure can also be exerted in solids, such as when you press your hand against a wall. The force you apply is spread over the surface of your hand, creating pressure on the wall.
Pressure has many applications in various fields, from physics and engineering to meteorology and medicine. Understanding pressure is crucial in designing structures, predicting weather patterns, and even explaining biological processes.
Ancient Beginnings: Early Concepts of Pressure
The concept of pressure has been recognized since ancient times, although the means to quantify it were rudimentary compared to today’s sophisticated instruments. Greek philosopher and mathematician Mr. Archimedes, in the 3rd century BCE, laid the groundwork for understanding buoyancy and hydrostatic pressure. His principle of buoyancy demonstrated the force exerted by a fluid on an immersed object, showcasing the effects of pressure.
17th Century: The Birth of Pressure Measurement
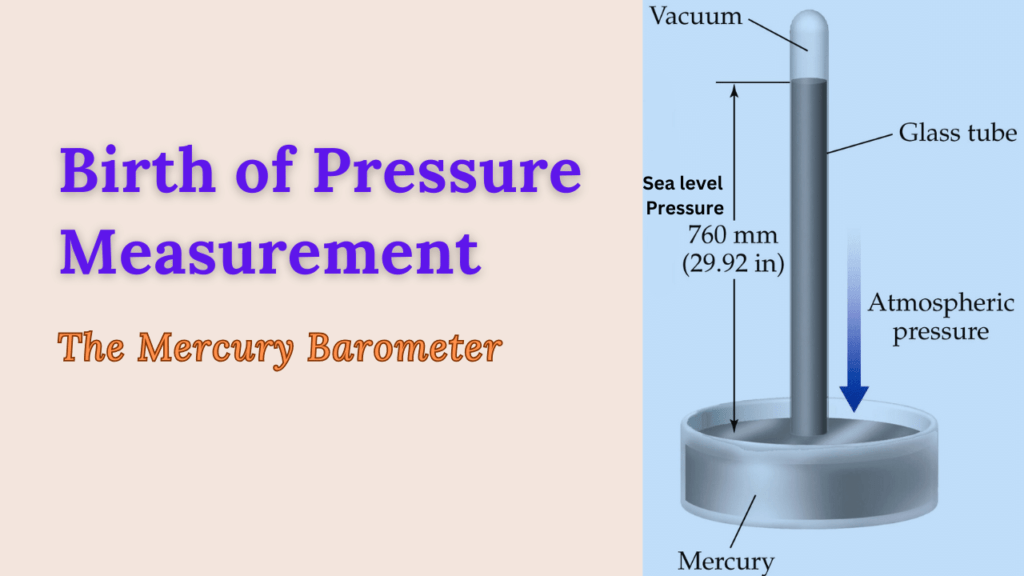
The 17th century marked a pivotal period in the development of pressure measurement techniques. Mr. Evangelista Torricelli, an Italian physicist and mathematician, famously conducted the mercury barometer experiment in 1643. By filling a glass tube with mercury and inverting it in a mercury-filled container, Torricelli observed that the mercury column fell to a certain height, leaving a vacuum at the top. This phenomenon demonstrated the pressure exerted by the atmosphere on the mercury, leading to the creation of the barometer – a precursor to pressure gauges.
18th Century: The Industrial Revolution and Progress
The Industrial Revolution brought about advancements in various fields, including pressure measurement. In the mid-18th century, French engineer Mr. Denis Papin developed the “steam digester,” a device that used steam pressure to cook food. While not a pressure gauge in the modern sense, it marked the practical application of steam pressure, a concept that would later become integral to industrial processes.
19th Century: Bourdon Tube Invention
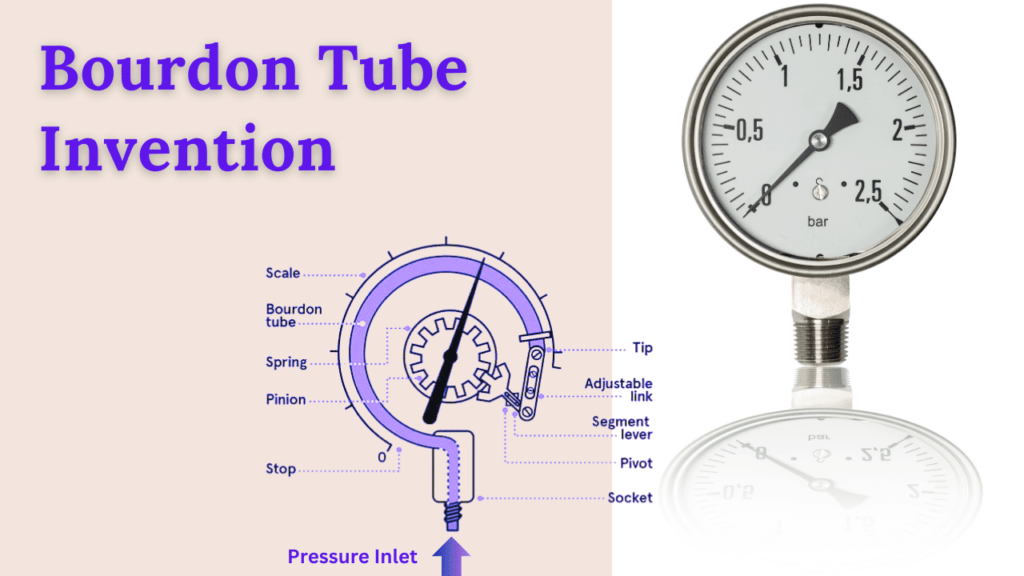
The 19th century saw significant strides in pressure gauge technology, culminating in the invention of the Bourdon tube by French engineer Mr. Eugène Bourdon in 1849. The Bourdon tube, a curved tube that straightens under pressure, was a groundbreaking innovation. As pressure increased, the tube’s movement could be linked to a pointer, providing a visual pressure reading. This invention revolutionized pressure measurement, and Bourdon gauges became the foundation for many subsequent pressure gauge designs.
20th Century: Advancements in Design and Applications
The 20th century brought remarkable developments in pressure gauge design, materials, and applications. The incorporation of diaphragms and other elastic elements enabled accurate pressure measurement in a wider range of conditions. Pressure gauges found their place in various industries, from manufacturing to aviation, ensuring safe operations and efficient processes.
Modern Era: Digital Precision and Automation
As technology advanced, pressure gauges underwent a digital transformation. Digital pressure gauges emerged, equipped with transducers that convert pressure into electrical signals. These signals are processed and displayed digitally, offering higher precision and often including features such as data logging and remote monitoring. This digital evolution aligns with the increasing demand for automation and real-time data in modern industrial processes.
Types of Pressure Elements
Pressure gauges utilize different types of pressure elements to measure pressure accurately. Some common pressure elements include:
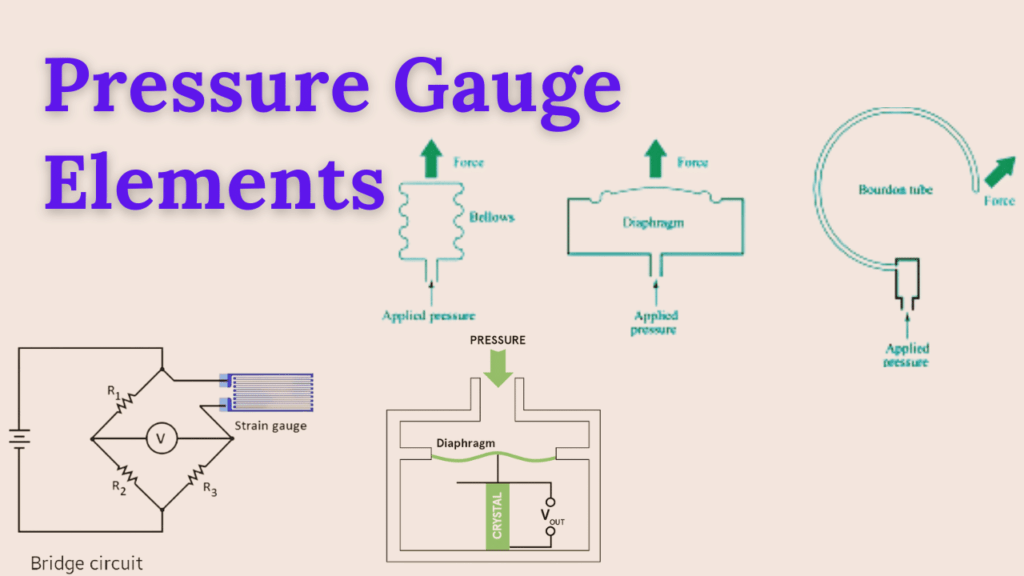
Bourdon Tube: The Bourdon tube is a curved metal tube that straightens when subjected to pressure, leading to the movement of a pointer on the gauge’s dial.
Diaphragm: Diaphragm pressure elements use a flexible diaphragm that deflects under pressure. This deflection is translated into a mechanical or electrical signal for pressure measurement.
Bellows: Bellows are collapsible, accordion-like structures that expand or contract with changes in pressure, indicating pressure variations on the gauge.
Piston and Cylinder: This mechanism involves the movement of a piston inside a cylinder due to pressure changes. The piston’s movement is then linked to the gauge pointer.
Strain Gauge: A strain gauge is an electronic pressure element that uses the deformation of a thin metallic strip under pressure to measure strain, which is then converted into an electrical signal for pressure measurement.
Piezoelectric Crystal: Some modern pressure gauges use piezoelectric crystals that generate an electrical charge when subjected to pressure. This charge is converted into a pressure reading.
Types of Pressure Gauges
Pressure gauges have evolved to suit diverse industrial needs. Some common types include:
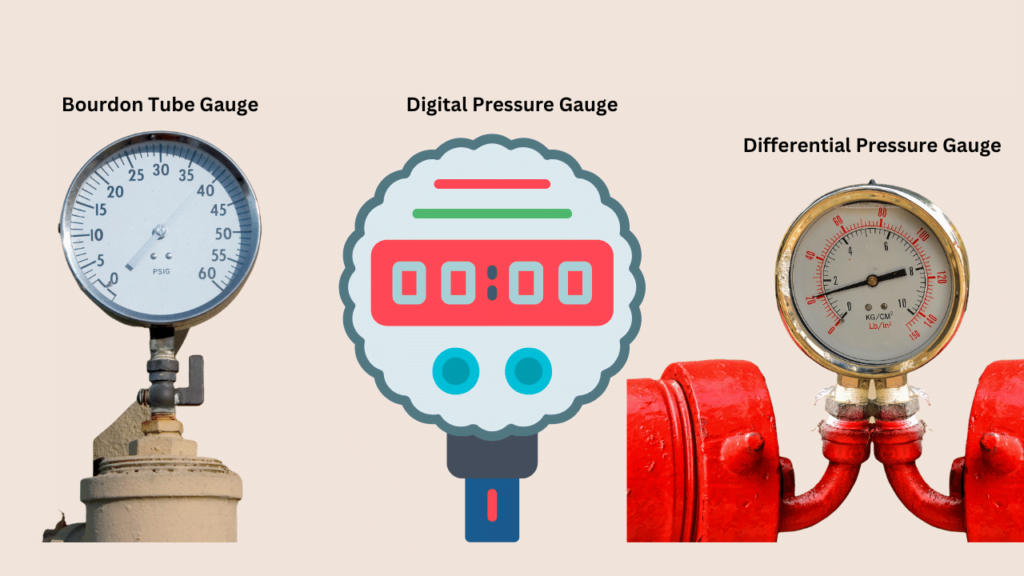
Bourdon Tube Gauges: The Bourdon tube, still widely used, remains a testament to the enduring legacy of Eugène Bourdon. Its simplicity and reliability make it suitable for various applications.
Diaphragm Gauges: Diaphragm-based designs excel in measuring low pressures or when contact with the process fluid needs to be minimized. They find utility in industries dealing with sensitive materials.
Differential Pressure Gauges: With the growth of complex industrial processes, the need to measure pressure differences arose. Differential pressure gauges fulfill this role, aiding in the efficient functioning of such processes.
Digital Pressure Gauges: The digital age brought about accurate, easy-to-read digital pressure gauges. They provide precise measurements, data logging, and remote monitoring capabilities, meeting the demands of modern industries.
Importance in Industrial Applications
Pressure gauges play a critical role in industrial applications for several reasons:
Safety: Many industrial processes involve working with high-pressure systems. Monitoring pressure is crucial to prevent overpressure situations that could lead to explosions or other hazardous incidents.
Quality Control: In manufacturing processes, maintaining consistent pressure levels is often essential to ensure product quality. Pressure gauges help operators maintain the desired pressure conditions for optimal results.
Equipment Efficiency: Pressure imbalances can lead to inefficient operation of machinery and systems. Pressure gauges help operators identify deviations from the optimal pressure range, allowing for timely adjustments and preventing energy wastage.
Preventive Maintenance: Pressure gauges provide early warnings about pressure fluctuations, leaks, or blockages. This information enables maintenance teams to address issues before they escalate into costly breakdowns.
Process Optimization: Certain industrial processes require specific pressure levels for maximum efficiency. Pressure gauges allow operators to fine-tune processes to achieve the desired outcomes.
Installation and Maintenance
For pressure gauges to provide accurate readings consistently, proper installation and regular maintenance are crucial. Some best practices include:
Correct Mounting: Pressure gauges should be mounted vertically with the dial facing the operator for easy reading. The connection to the process line should be tight to prevent leaks.
Calibration: Regular calibration ensures that pressure gauges provide accurate readings. Calibration should be performed by qualified professionals using standard equipment.
Protection: Pressure gauges protector or saver should be equipped to prevent damage from excessive pressure or temperature where are required.
Regular Inspection: Pressure gauges should be visually inspected for any signs of damage, corrosion, or wear. Damaged gauges should be replaced or repaired promptly.
Conclusion
Pressure gauges have come a long way from their humble beginnings as mercury barometers and early pressure indicators. The historical evolution of pressure measurement has led to the development of various types of pressure gauges, each tailored to specific industrial needs. Today, these instruments are indispensable tools in ensuring the safety, efficiency, and reliability of industrial processes. As industries continue to advance, pressure gauges will remain an integral part of maintaining optimal and safe operating conditions, reflecting the journey of innovation and progress that has shaped their role in modern engineering.